Skloubení poctivého řemesla a moderních technologií
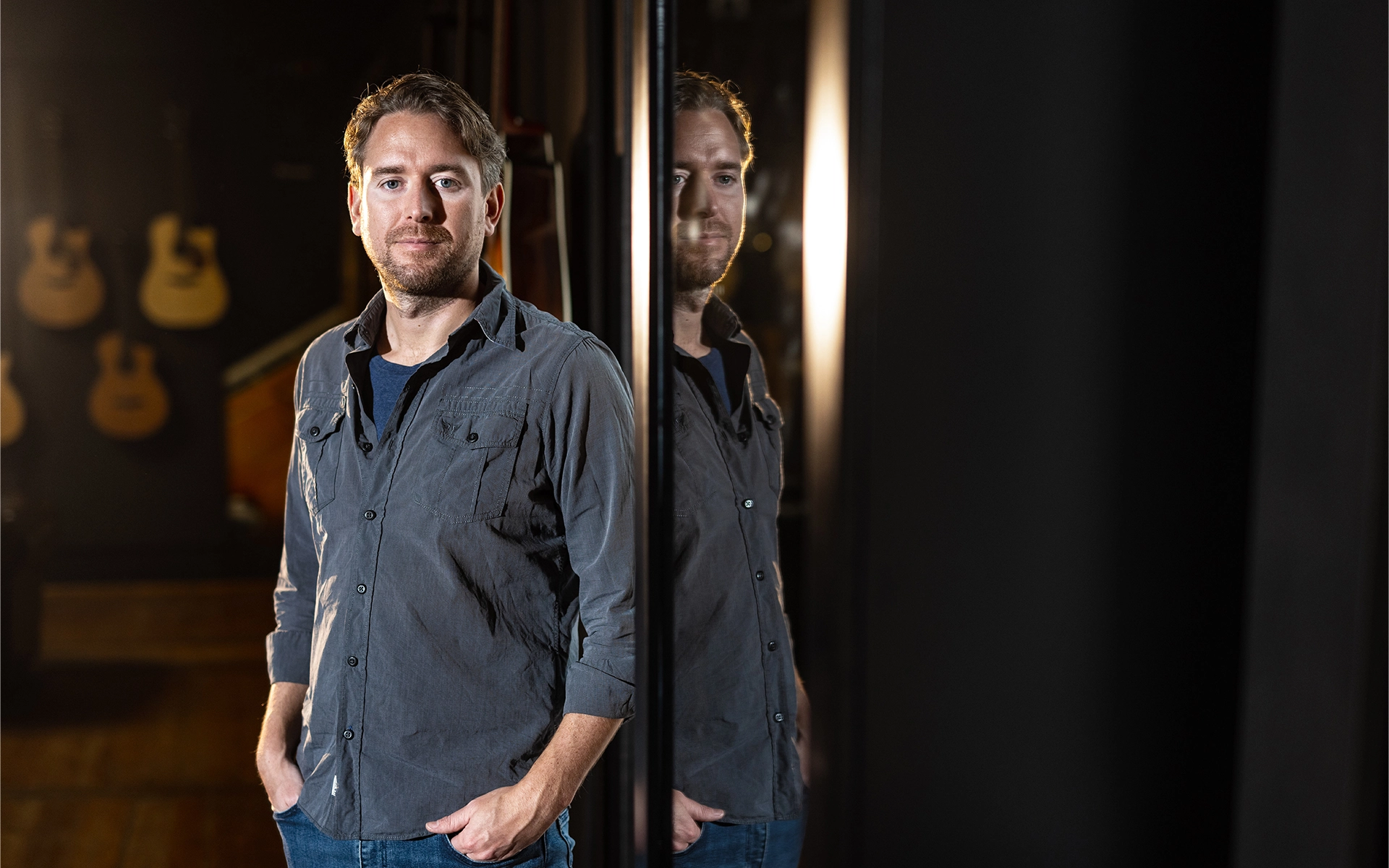
V rámci naší spolupráce s výrobcem prémiových akustických kytar Furch, známých dnes mezi muzikanty po celém světě, jsme měli možnost nahlédnout do výroby kytar v komplexu zrekonstruovaného bývalého mlýna ve Velkých Němčicích. Výrobou nás provedl Petr Furch, který se po svém otci Františku Furchovi ujal vedení společnosti a nadále pokračuje v jejím rozvoji. Postupně propojuje tradiční řemeslnou výrobu s nejmodernějšími obráběcími CNC technologiemi. Vedle výzkumného oddělení, které vyvinulo unikátní technologii UV lakování umožňující dosáhnout tenké vrstvy laku za současného zvýšení tvrdosti a brilantnějších zvukových vlastností, přišlo s novým designem odlehčeného žebrování se zvýšenou tuhostí či inovativní kompozitní konstrukci krku Furch CNR System®. V několika posledních letech pracuje na významné automatizaci a robotizaci výroby. Zároveň si ale uvědomuje nezbytnost využívání lidského řemeslného umu. Rádi jsme využili pozvání do výroby a Petra Furcha vyzpovídali.
V rámci naší spolupráce s výrobcem prémiových akustických kytar Furch, známých dnes mezi muzikanty po celém světě, jsme měli možnost nahlédnout do výroby kytar v komplexu zrekonstruovaného bývalého mlýna ve Velkých Němčicích. Výrobou nás provedl Petr Furch, který se po svém otci Františku Furchovi ujal vedení společnosti a nadále pokračuje v jejím rozvoji. Postupně propojuje tradiční řemeslnou výrobu s nejmodernějšími obráběcími CNC technologiemi. Vedle výzkumného oddělení, které vyvinulo unikátní technologii UV lakování umožňující dosáhnout tenké vrstvy laku za současného zvýšení tvrdosti a brilantnějších zvukových vlastností, přišlo s novým designem odlehčeného žebrování se zvýšenou tuhostí či inovativní kompozitní konstrukci krku Furch CNR System®. V několika posledních letech pracuje na významné automatizaci a robotizaci výroby. Zároveň si ale uvědomuje nezbytnost využívání lidského řemeslného umu. Rádi jsme využili pozvání do výroby a Petra Furcha vyzpovídali.
Jak a kdy vznikla myšlenka vyrábět akustické kytary?
První kytaru vyrobil můj otec v roce 1981. Byl aktivním muzikantem ve folkové kapele. V tehdejší době byl u nás nedostatek kvalitních nástrojů. Trendy byla zrovna roundbacková kytara, což je kytara s vyboulenou zadní deskou, vyráběnou z plastu vakuovým lisováním. Byl to americký vynález značky Ovation a sehnat ji u nás bylo takřka nemožné. Otec ji viděl v nejrůznějších časopisech a novinách a řekl si, že si ji zkusí vyrobit sám. Připravil si sádrové kopyto na zadní stranu kytary, kterou následně udělal ze sklolaminátu. Koupil staré piano, ze kterého pak vyrobil přední desku kytary. Z piana mu pak zbyl ještě materiál na dvě další kytary. Když ji vzal na zkoušku ukázat kamarádům, chtěli ji hned také. Ptali se, kolik by za ní chtěl a ať jim také vyrobí takovou. To byly vlastně první neoficiální objednávky a takhle to vlastě všechno začalo.
Jaké to bylo za socialismu vyrábět kytary?
To je spíš otázka na otce, ale co od něj vím, tak ho to v podstatě bavilo. Nešlo ale jen o samotnou výrobu katary jako takové, ale o problematiku všech těch věcí kolem. Jako zámečníka ho bavilo vymýšlet nové věci, jak si výrobu usnadnit. Vymýšlel přípravky, které mu umožňovaly zbavovat se složité ruční práce. Třeba, jak ofrézovat kobylku, aby ji nemusel pokaždé celou vyřezávat ručně. Nechci mluvit za něj, ale myslím, že tohle bylo jeho hnacím motorem. Vycházím i ze své zkušenosti, když jsem do firmy v roce 2006 nastupoval já. Tehdy mě otec motivoval, abych se profesně věnoval kytařině. Zdědil jsem po něm technický talent a dokázal jsem si představit vychytávky a přípravky, které usnadňovaly výrobu. Když jsem k jejich použití dostal svolení, zavedli jsme je a mým kolegům to pomáhalo dělat rychleji a kvalitněji. Dělat tahle vylepšení, to bylo a do dneška je mým hnacím motorem. A předpokládám, že stejně tak to měl otec.
Podnikání to ale asi v té době ještě nebylo. To přišlo až po revoluci, je to tak?
Za socialismu se oficiálně podnikat nedalo, takže to dělal po večerech. Když došel z práce, tak si jako dítě pamatuju, že šel do garáže a tam vyráběl všechno možné na kytary. Jako děti jsme tomu ještě moc nerozuměli. Když těsně před pádem režimu došlo k uvolnění, rozhodl se, že bude podnikat a vyrábět kytary. Po revoluci už to přišlo automaticky. Založil živnost, najal první lidi a první prostory tady u nás v Němčicích.
Kde jste s podnikáním začínali, než jste se dostali do stávajících prostor?
Chvilku měl otec pronajatý prostor ve vedlejší budově, které se říká zámek. Tam byl do poloviny devadesátých let. Následně se přestěhoval sem do bývalého mlýna, kde byly zcela volné prostory, které si pronajal. Následně se provoz dále rozšiřoval. Později po roce 2000 jsme se přestěhovali do vedlejší budovy sýpky, kde je výroba dodnes. V plánu máme během dvou dalších let přistavit zcela nové výrobní haly. Potřebujeme totiž prostory o nějakých 1 000 m². Chtěli bychom to vše udržet tady na jednom místě. Ve stávajících prostorách zůstane výroba menších dílů, jako jsou přední desky. Výrazně rozšířit ale rozhodně potřebujeme lakovnu, obráběcí dílny, expedici a skladové prostory. Ty bychom rádi měli v moderní budově, která bude mít trošku lepší technické parametry třeba, co se týká například výše stropu. To je potřebné pro větší a těžší technologie, které se nám nevejdou do stávajících prostor.
Když se vrátím zpět ke kytarám, co je dělá pro zákazníky tak výjimečnými?
Myslím, že naše výjimečnost je v unikátním zvuku. Z počátku jsme ke zvuku přistupovali intuitivně, společně s otcem máme stejnou představu o jeho výsledné podobě. Postupně jsme dospěli, dá se říci, k takovému “Furch” zvuku. Co je podstatné, že ho umíme replikovat napříč našimi řadami a typy kytar. Náš zvuk nedovede napodobit žádná jiná firma, protože to obnáší vyřešení mnoha parametrů. Naši zákazníci ho rozeznávají mezi ostatními a líbí se jim náš přístup k němu. To je vidět třeba i dle recenzí a testů na YouTubu nebo jiných webových platformách. Dalším klíčovým parametrem je dlouhodobé udržení vysoké úrovně kvality. Právě vysoká přesnost a kvalita zpracování souvisí s výsledným zvukem nástroje. Díky používaným technologiím není až zas tak problematické a cenově náročnější nastavit větší přesnost ve výrobě. Jen je to potřeba dopředu vše dobře promyslet.
Kolik řad kytar aktuálně zákazníkům nabízíte a jaká je vaše roční produkce?
Máme několik základních řad. Daný typ pak dokážeme vyrobit ve všech možných variantách, kterých může být až několik stovek. Základní rozčlenění máme dané podle barev. Jako základní řadu nabízíme Violet, pak následují řady Blue, Green, Yellow, Orange a Red. K tomu máme ještě kytary řady Vintage a Grand Nylon. Zapomenout nesmím na zakázkovou řadu Rainbow. Tam je možno si poskládat různé typy materiálu přední desky, zadní desky, lemování, dekorací všeho možného typu. Tyto jsou doplněny ještě jedním velice populárním modelem. To je naše cestovní kytara, kterých vyrobíme zhruba 600 ročně. Celkově se teď naše produkce pohybuje někde kolem 8 000 kytar ročně. Záleží to na tom, jaký poměr modelů vyrábíme. Jestli vyrábíme větší část dražších kytar nebo větší část levnějších kytar. U dražších kytar je samozřejmě vyšší náročnost na ruční práce, a tudíž jich pak stíháme vyrábět méně.
Prioritou tedy není dosažení kvantity výroby?
Ani prioritou, ani cílem. Důležitá je pro nás především kvalita našich nástrojů. Momentálně se kapacita produkce pohybuje někde mezi sedmi až osmi, v extrému, kdybychom vyráběli ty nejlevnější řady, k devíti tisícům kytar. Aktuální denní kapacita je 35 kytar a tu se nyní snažíme v rámci letošního roku nastavit na 57 kytar. Kdybychom následně celý rok pokračovali v těchto počtech, mohli bychom dosáhnout výroby 13 000 kytar.
Co je impulsem k vývoji zcela nového modelu kytary, co její vznik obnáší a jak dlouho to trvá?
Všechny naše modely již mají nějakou evoluci za sebou. Postupujeme totiž spíše evolučním způsobem než revolučním. Kytary vychází z nějakých trendů a nesou nějaká očekávání muzikanta. Takže my postupujeme spíše menšími kroky k tomu, abychom se s každým naším modelem dostali blíž našemu ideálu zvuku. Máme modely, které mají svůj potenciál využitý již velice dobře, těm není potřeba se tolik věnovat. Ale pak jsou modely, ve kterých vidíme příležitost na vylepšení a zde pracujeme na dalším vývoji. Nepostupujeme tedy tak, že bychom najednou představili třeba nový model. Že toto je ta novinka, kde najednou máme o 15 % lepší zvuk, hlasitost, sustain, vyváženost atp. Můžete mít pořád model Violet, který se tak jmenoval i před tím, ale my jsme do něj v určité fázi a od určitého sériového čísla vylepšení prostě začali implementovat. Děláme to v momentě, kdy už máme odzkoušeno, že dané vylepšení je skutečným krokem kupředu. Z tohoto důvodu vyrábíme vzorky, vyzkoušíme třeba tři postupy, kterými se můžeme dostat k lepšímu zvuku. Může to být způsob ladění přední rezonanční desky, může to být změna žebrování, nebo i povrchová úprava si s sebou nese svá specifika. Pro vyzkoušení, že to funguje, je potřeba vyrobit několik totožných exemplářů s touto změnou, abychom eliminovaly nějakou, třeba výrobní, nepřesnost. Následně dojde k porovnání, jestli jsme skutečně dosáhli toho vylepšení nebo ne. Pokud dojde k odsouhlasení, následuje uvolnění do výroby. Tyto změny ale neinzerujeme, neděláme na ně kampaně. Interně se změna pouze zaznamenává do seznamu sériových čísel. Za posledních deset let je to hodně dlouhý seznam čísel. Interně o významnějších změnách informujeme naši distribuční síť. Náročnost a délka vylepšení je závislá, do jakého detailu až chceme jít a jak se daná věc rychle daří řešit. Může to trvat tři měsíce, ale klidně i dva roky.
Velkou a výraznou inovaci jsme ale přinesli v druhé polovině minulého roku díky ergonomickému prvku “Bevel Duo”. Je to takové zkosení na těle kytary, které má hlavně ergonomický význam. Pokud hrajete na kytaru více než tři hodiny začnou vás od hrany kytary bolet žebra a ruka. Snažili jsme se tedy udělat ergonomické změny pro přívětivější držení, kdy jsme lehce srazili hrany těla kytary. Kromě ergonomického efektu to přineslo i designovou změnu, která na kytaře vypadá opravdu skvěle. Nástroj se výrazně pocitově zmenšil, i když se jednalo o milimetry. Zde se jednalo o výraznou a pro výrobu komplikovanou změnu, která se stala zcela novým modelem a její uvedení na trh bylo marketingově podpořeno.
Nakolik při výrobě sázíte na tradiční postupy a na kolik využíváte nových pokrokových technologií?
Na to se dá odpovědět takovým příběhem. Když jsem se jako teenager rozhodoval, na jakou školu po základce půjdu dál, chtěl jsme studovat IT. Doma mi to bylo otcem dost explicitně zakázáno s tím, že na počítači chce pracovat každý a že nebude pro tyhle lidi dostatek práce. Nakonec jsme se dohodli, že půjdu na uměleckého truhláře. Když jsem se pak taťky ptal, jestli nemám jít přímo na kytaráře, abych pak do budoucna mohl zapojit do firmy, tak si pamatuji, jak říkal, že určitě ne. Protože co se učí na kytarářských školách je tradiční způsob, a on už v té době byl s výrobou někde jinde. Inovoval strašně moc výrobních postupů, hledal lepší a efektivnější řešení pro dosažení ještě lepšího výsledku. To bylo někdy kolem roku 2000.
V dnešní době si troufám říct, že jsme technologicky nejvyspělejší kytarovou firmou na světě, protože naše výrobní postupy a technologie, které jsme zavedli, jsem zatím u našich konkurentů nikde neviděl. Je to dáno i tím, že mě technologie opravdu moc baví a otec mě vlastně k tomu od začátku vedl a byl k moderním postupům otevřený. Počítače sice nejsou jeho parketa, ale díky vyučené profesi zámečníka má dokonalou představivost o materiálech, jak je správně opracovávat a obrábět. Ví, co se s materiálem děje, když se nějakou formou zpracovává, zatěžuje, zahřívá, chladí atp. Díky tomu, když jsem se začal angažovat ve výrobě, byl otevřený i použití CNC strojů. Protože jsme v nich oba viděli obrovský potenciál, začali jsme je u nás do výroby zavádět a celý proces postupně automatizovat. To samozřejmě vyžadovalo přemýšlení o předchozích i následujících procesech, aby na sebe vše navazovalo. A také když obrábím jeden kus, tak aby byl stejnou technologií obráběn i ten druhý protikus, aby do sebe všechno přesně a pěkně pasovalo. Během let jsme tady hodně těch postupů zcela přetvořili právě pomocí technologií. A hlavní prioritou bylo pro nás vždy zvýšení kvality a až následně produktivity, ta s tím většinou přišla následně sama. Měli jsme samozřejmě spočítáno, že se nám to vyplatí. V rámci automatizace a jejího využívání jsme prošli čtyřmi zásadními kroky.
Můžeme se u těchto kroků ve stručnosti zastavit a popsat si je?
Prvním krokem bylo seznámení se a započetí s využíváním tří osého CNC obrábění, protože to pro mě byl tehdy zcela nový svět, který jsem se musel naučit. Předtím jsem si úplně nedokázal představit, jak to funguje. Vůbec pochopení světa XYZ a jak to vše naprogramovat, co k tomu použít, jak se dělají modely, podle kterých potom ty mašinky můžou jet. To byla první zásadní etapa.
Pak přišla etapa pěti osého obrábění, které samozřejmě vychází z toho tří osého, ale je to o další dvě úrovně komplikovanější, protože tam už se naklání ty jednotlivé osy, dá se naklánět frézovací hlava. Díky tomu tak lze přistupovat k obrobku z různých stran, je to úplně něco nového, co se programuje odlišně. To bylo další důležitou etapou.
Pak přišla robotika, kdy jsme začali s průmyslovými roboty typu ABB, kdy je logika jejich fungování opět zcela jiná. CNCéčko je taková mašina, kterou člověk koupí a ona je hotová, ale když stavíte robotickou buňku, tak to musíte všechno okolo vymyslet a vůbec ten postup, co se tam s tím bude dít a jak se to vše bude hýbat. To je potřeba vymyslet úplně od začátku, takže opět něco zcela nového, naučit se v tomto duchu přemýšlet.
A teď ten nejčerstvější, to je čtvrtý krok – čtvrtá etapa, který jsem objevil a který je pro nás tak důležitý. To jsou kolaborativní roboty, které vychází z průmyslových robotů. Ty pro firmu našeho typu, která má stále velký podíl ruční práce, ale chce více automatizovat, zvyšovat přesnost a dělat pro lidi práci pohodlnější, přináší strašně jednoduchou možnost integrace zařízení.
Jaké byly vaše první zkušenosti s kolaborativními roboty?
Já jsem se s kolaborativními roboty setkal prvně právě přes Servind. To díky tomu, že jsem do světa vyslal informaci, že chci řešit broušení dřevěného a lakovaného povrchu. Interní analýzou jsem zjistil, že třetina času, kterou pálíme při výrobě, je spojená nějakým způsobem právě s broušením. A na broušení jsme tenkrát neměli žádnou technologii. Uměli jsme obrábění pomocí CNCéček, věděli jsme, jak aplikovat lakování nebo leštění povrchu. Ale broušení, ať už nějakých malých dílů, jako kobylek nebo krku, nebo prostě těla kytary nebo mezibrusů laků, na to jsme neměli žádné řešení. Sešlo se několik zajímavých a jedno z nich byla robotická brusná hlavice Mirka. Ta mi byla prezentována právě Servindem, jako distributorem Mirky. Brusku jsem chápal, ale proniknout jsem potřeboval do fungování kolaborativních robotů. Ty drží tu brusku a umožňují její řízený pohyb. Na dané prezentaci byl i člověk z Amtechu, distributor kolaborativních robotů Universal Robots, který se Servindem úzce spolupracuje. Takže se tehdy ten rozhovor přesunul ke kolaborativnímu robotovi. Zásadní pro mě tehdy bylo, jak jednoduché je jeho ovládání, které bylo ukázáno v tutoriálech na internetu, kde bylo vidět jak, konkrétně to URko funguje. Na základě tohoto setkání jsme se domluvili, že bych si tohoto robota zapůjčil a zkusil jsem si s ním pohrát. A protože u nás měla být zrovna celozávodní dvoutýdenní dovolená, že si ho nainstaluji na jednom pracovišti, kde si sám zkusím připravit program, protože tak, jak mi to bylo vysvětleno, bych to měl zvládnout.
Prošel jsem několik málo tutoriálů a učebních programů co má URko na webu. Nechal jsem si poslat robota jenom v balíku a nainstalovali jsme ho u nás na jedno pracoviště. Během dvou dní, netrvalo mi to myslím ani dva celé dny, jsem udělal program na broušení zadní desky kytary. Takže během takto krátké doby jsem sám bez nějaké vleklé průpravy, aniž bych musel chodit na nějaká školení, připravil svůj program. To mi potvrdilo, že to je to, co potřebujeme, abychom robotiku mohli ve firmě aplikovat výrazně odvážnějším tempem.
V čem vidíte výhody oproti klasickým průmyslovým robotům?
Problém u průmyslových robotů je v tom, že technolog, který ví, co potřebuje dělat, musí danou informaci robotovi předat prostřednictvím nějakého programátora. Programátor a technolog se ale většinou nesetkávají v jedné osobě, protože mají zcela odlišné způsoby myšlení. Je tedy potřeba přetlumočit potřeby technologa programátorovi a ten je musí naprogramovat do zařízení. Kdežto vlastně u kolaborativních robotů a způsobu, jakým oni se učí, vlastně programátora nepotřebujete. Stačí vám technolog, který je zaučený v tom, jak to naučit robota, což je strašně jednoduchá věc, kde nepotřebujete znalosti programování a programovacích jazyků. On dané požadavky rovnou předává tomu robotovi a tím se ušetří strašně moc času, nákladů a vše se dá najednou realizovat mnohem rychleji a levněji. To je na tom úžasné. Já to vlastně přirovnávám k tomu, když byly Nokie a najednou přišel iPhone. Tak velký je to posun v robotice. Jakmile jsem tento čtvrtý svět objevil a samozřejmě i díky zvýšené poptávce po kytarách během Covidu se nám otevřely další dveře. Opřeli jsme se do toho a během dvou let nainstalovali celkem devět robotů. To věřím, že je potvrzení důvěry, kterou v robotizaci mám. Skutečně vidím, že to je produktivní řešení pomáhající držet kvalitu a je to pro nás strašně důležité. Myslím, že každý, kdo chce do budoucna přežít, se musí tímto směrem vydat.
Na co je využíváno robotické pracoviště, které u vás instalovali kolegové z našeho oddělení Business Developmentu?
Mezibrusy a broušení patří k fyzicky velmi náročným pracím a navíc jsou také náročné na přesnost. Proto jsme pro brusnou aplikaci mezivrstev a finálního tvrdého UV laku hledali robotické řešení a v tuto chvíli máme instalovánu robotickou brusnou buňku Mirka – Universal Robots. Na první pohled by se mohlo zdát, že se jedná o jednoduchou aplikaci, ale díky opravdu tvrdému laku a členitým tělům kytar se ve finále jedná o složité brusné operace. Troufám si říct, že po nějakém odladění tato robotická buňka zastane 70-80 % práce a 20-30 % zbyde na doladění jemných detailů pomocí ručního broušení, tzv. finishing touch. Hlavně v místech, která nejsou pro robota dobře přístupná. To je ale právě ta práce, které by se měl věnovat kvalifikovaný personál, protože s detaily dovede pracovat lépe a tato práce je pro něj navíc méně fyzicky náročná.
Kromě broušení spolupracujeme i v oblasti lakovacích materiálů od německé společnosti Hesse Lignal, nedá mi proto nezeptat se i na proces lakování.
Provádíme dva typy lakování. Jednodušší povrchovou úpravu nazýváme Open-Pore Finish. To je docela tenoučká vrstva kolem 60 mikronů, při které se záměrně nesnažíme zalévat póry. Tato úprava má takový dost přírodní charakter a vypadá opravdu pěkně, zvlášť u těch exotičtějších materiálů jako je třeba mahagon, kde jdou krásně vidět jeho póry. Naší vlajkovou povrchovou úpravou je ale Full-Pore Finish, nejčastěji ve vysokém lesku, vyleštěného jako zrcadlo. Tato povrchová úprava se skládá až z deseti jednotlivých nástřiků. Deset vrstev se může zdát hodně, ale nanášíme je v co nejtenčích vrstvách. Celkem je to kolem 180 mikronů a povrch musí být vyveden v té nejvyšší kvalitě. Jedná se o UV lak a vyvíjeli jsme ho na míru speciálně pro nás ve spolupráci se společností Hesse Lignal. Na trhu je množství kvalitních lakovacích materiálů na dřevo, ale ty jsou vyvíjeny primárně pro nábytkářský průmysl a my potřebujeme lak, který nepotlačuje, ale právě vylepší, akustické vlastnosti kytary.
Jak probíhá samotné lakování?
Lakování probíhá komplet roboticky. Tzn., že poté, co operátor umístí kytary do vstupního zásobníku lakovací buňky, si je odtud odebere robot a přesune je do prostoru lakovací stěny, kde na ně vzápětí aplikuje vrstvu laku. Po nastříkání je dále přenáší do UV sušicí kabiny, kde dochází k vytvrzování. Poté robot ukládá kytary zpět do manipulačního zásobníku. Z tohoto místa je operátor převáží na mezibroušení či finální broušení.
Právě použití robotického lakování umožnuje dříve zmiňované nanášení požadovaných tenkých vrstev. Oproti lidské práci se lakovací dráhy robota dají podstatně lépe optimalizovat, protože je daný pohyb schopen vždy přesně opakovat a zachovat i jeho stálou rychlost. Toho při lakování využíváme, ať už za účelem dosažení vysoké kvality lakování, tak úspory lakovacího materiálu. Tím, že se používá UV lak, který nevytvrdne, dokud není aktivován UV zářením, vzniklé přestřiky sbíráme, filtrujeme a znovu používáme. Předpokladem je, že zařízení je celé nerezové, lak po něm steče a po přefiltrování přes dva filtry je nadále krásně čistý a nemění konzistenci. Takto ušetřený materiál pak přidáváme do základu, ne ale již do lesku.
Když správně využijeme možnosti technologií, jako jsou vysoká opakovatelnost a možnost vykonávání vysoce fyzicky náročné práce, a správně je poskládáme se schopnostmi člověka, které jsou stále nenahraditelné, můžeme dle mého názoru dosáhnout vysoké kvality a efektivity produkce. A my tady ten princip využíváme vlastně skoro ve všech postupech.
Jaké máte letos ve firmě další plány?
V letošním roce jsme si dali za cíl navýšit denní výrobu o 63 %. Chtěli bychom se k tomuto číslu dostat v září, ale je to závislé na mnoha věcech. Jednou z nich je, abychom tady měli nainstalované a odladěné některé automatizace, které jsme si vymysleli během posledních několika let a zhruba před rokem jsme si odsouhlasili, že se do nich pustíme. Jejich realizace je dnes možná díky zvýšené poptávce a prodejům během Covidu. Jedno z pracovišť se týká broušení korpusů, to je naše další společná realizace robotické buňky. Další pracoviště se týká sestavení celého korpusu kytary – tedy vlastně sestavení přední desky, zadní desky, slepení s luby, včetně ofrézování různých dílů, nanesení lepidla. Tam jsme potřebovali použít průmyslového robota, který má vysokou nosnost. Dále probíhají instalace ještě dvou pracovišť, které děláme externě a kde rovněž používáme kolaborativní roboty Universal Robots. Jedno se již dolaďuje, druhé se instaluje a začneme ho nastavovat. Jedno pracoviště budeme nasazovat ještě interně. Zde se jedná o kopii jiného již používaného pracoviště.
A na co se můžeme těšit v budoucnosti?
Jak jsem již říkal, rádi bychom se dále rozšířili. To je podmínkou budoucího rozšiřování kapacity produkce. Předpokladem k tomu je, aby značka Furch byla celosvětově dostatečně známá a vyspělá. V Americe jsme v podstatě začínající firma, i když tam již náš marketing dělá dobrou práci. Zatím jsme tam takoví exoti, protože evropských firem, co vyrábí kytary tam moc není. V tomto prémiovém segmentu je u nich naprostá většina značek americká. Ale jde vidět, že i zdejší muzikanti schvalují náš přístup ke kvalitě, líbí se jim náš zvuk a filozofie, jak k němu přistupujeme. Když bychom byli na všech trzích známí jako v České republice, tak můj předpoklad našeho prodejního potenciálu je někde mezi 25 000 - 30 000 kytar za rok, pokud zachováme naše stávající portfolio. To je dlouhodobý cíl, kam směřujeme. Z toho důvodu nasazujeme ve výrobě nové technologie, abychom byly efektivnější a udrželi kvalitu. Díky tomu rovněž dokážeme udržet náklady i v dnešní době na dost dobré úrovni. Nemusíme ani přenášet veškeré zvyšování cen, třeba vstupních materiálů, na zákazníky. Zde vidím náš potenciál.
Co oceňujete na spolupráci se Servindem?
Od začátku jsme vzájemně věděli, že nasazení dané robotické buňky a odladění samotné pracovní operace bude velice náročné. To mi bylo jasné i vzhledem k tomu, že jsem již nějakou zkušenost s kolaborativní robotikou měl. Broušená vrstva laku je opravdu tenoučká, takže hrozí riziko probroušení, UV lak je extrémně tvrdý, tvary kytary složité. Ani jedna ze stran s touto konkrétní aplikací neměla přímou zkušenost, ale věřili jsme, že je jí daná technologie schopna dokázat. Vy jste věřili mé představě a já tomu, že to dokážete. Broušení mezivrstev laku byl pilotní projekt, bez možnosti použít zkušenosti z jiného historického projektu. Oceňuji, že i když jste tady strávili více času, než jsme obě strany předpokládali a bylo naplánováno, tak bylo vše dodrženo, jak jsme se domluvili a neodjeli jste do té doby, než byl výsledek k naší spokojenosti. K projektu jste přistoupili extrémně zodpovědně. To je důvod, proč jsem se rozhodl podepsat i pořízení dalšího pracoviště od vás.
Děkuju za rozhovor a přeji, ať se daří v dalším rozvoji.